Tube Laser Cutting Video On Youtube
Metal Tube Laser Cutting Machine Description
Wintek four-chuck metal tube laser cutting machine is specially designed for long parts processing, achieving no tailing, high efficiency and high stability processing effect. It is widely used in aerospace, automobile manufacturing, energy pipelines, mechanical processing and other fields.
Compared with the three-chuck machines, the four-chuck pipe cutter can realize the loading and processing of the next pipe on the loading side while unloading the workpiece, greatly improving production efficiency. The four-chuck structure can realize four chucks to clamp and cut at the same time, and there is no length limit for tailing processing, thus realizing real zero tailing processing under all working conditions!
The four-chuck tube laser cutting machine does not require manual intervention during the whole process of operation. The last two chucks can move freely to carry the finished products, ensuring that unloading is safe and avoiding the risk of personal injury.
Technical Parameters
The tube laser cutting machine is engineered for high-precision and efficient processing of various metal tubes. It offers advanced features to meet the demands of modern industrial applications, ensuring exceptional performance and accuracy. The following is an introduction to the parameters of the fiber laser tube cutting machine:
Model | WT12055T | WT12070T |
Max. processing tube length | 12500mm | 12500mm |
Cutting diameter | 20-550mm | 20-730mm |
Maximum tube weight | 3000kg | 3300kg |
Shortest remaining material | Zero tails | Zero tails |
Positioning accuracy | ±0.15mm/m | ±0.15mm/m |
Repositioning accuracy | ±0.15mm/m | ±0.15mm/m |
Max. Chuck rotating speed | 30r/min | 27r/min |
Y axis maximum speed | 50m/min | 45m/min |
X axis maximum acceleration | 0.3G | 0.3G |
20mm roundness | ≤0.15mm | ≤0.15mm |
20mm square diagonal size difference | ≤0.20mm | ≤0.20mm |
20mm square position size difference | ≤0.40mm | ≤0.40mm |
Dimensions | 32000*8490*3670mm | 32000*8500*4200mm |
Tube Laser Cutting Machine Sample
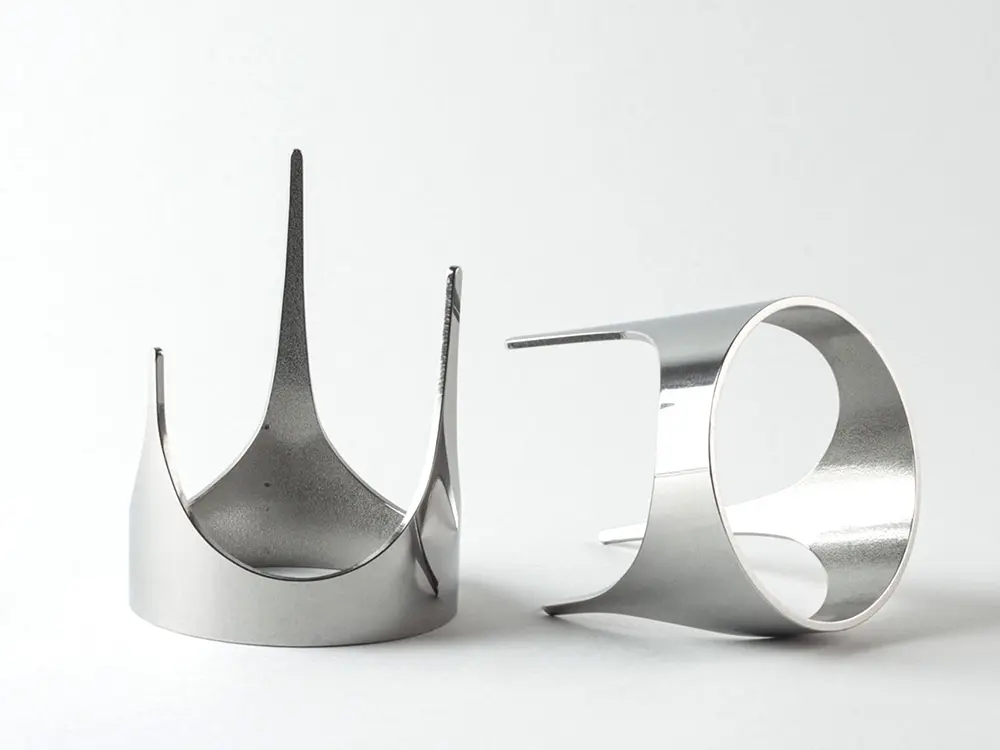
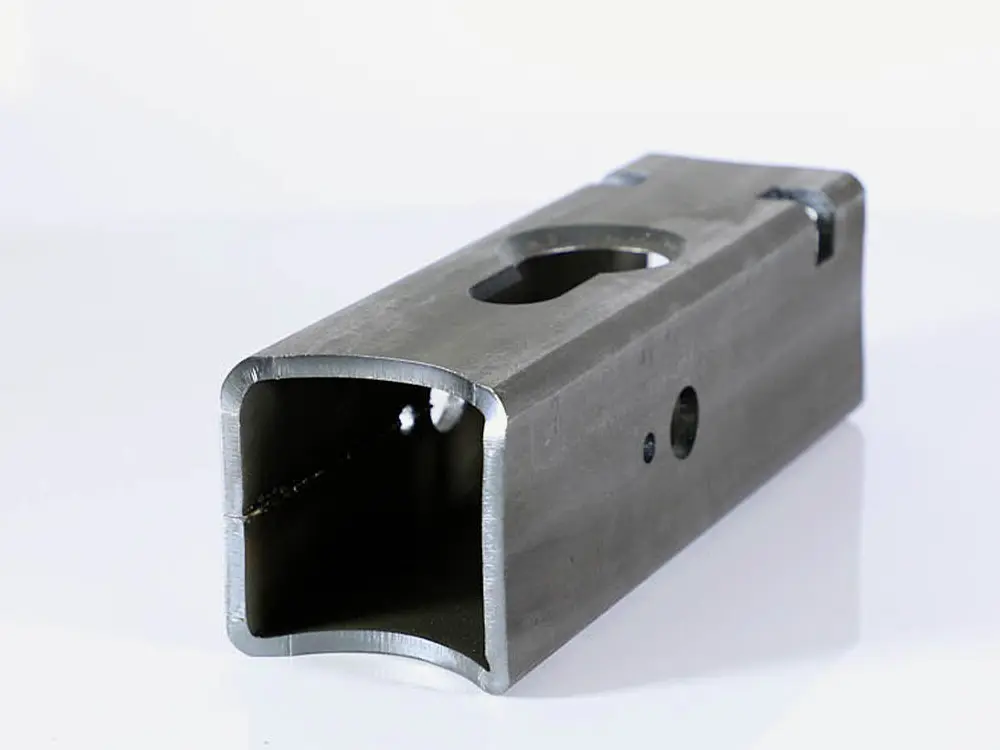
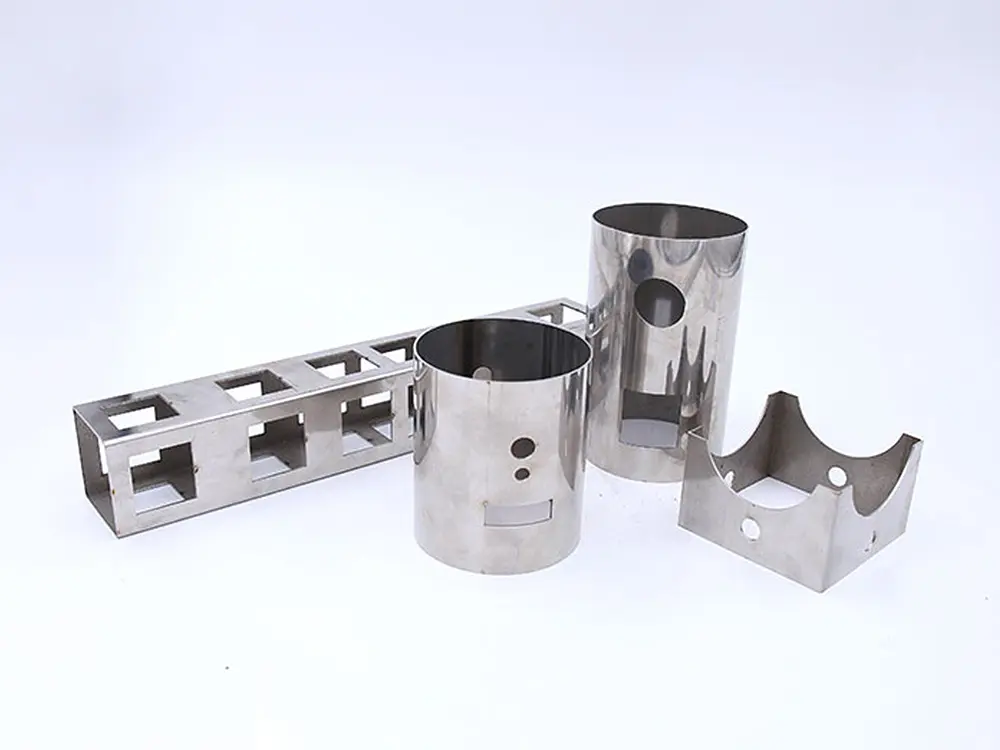
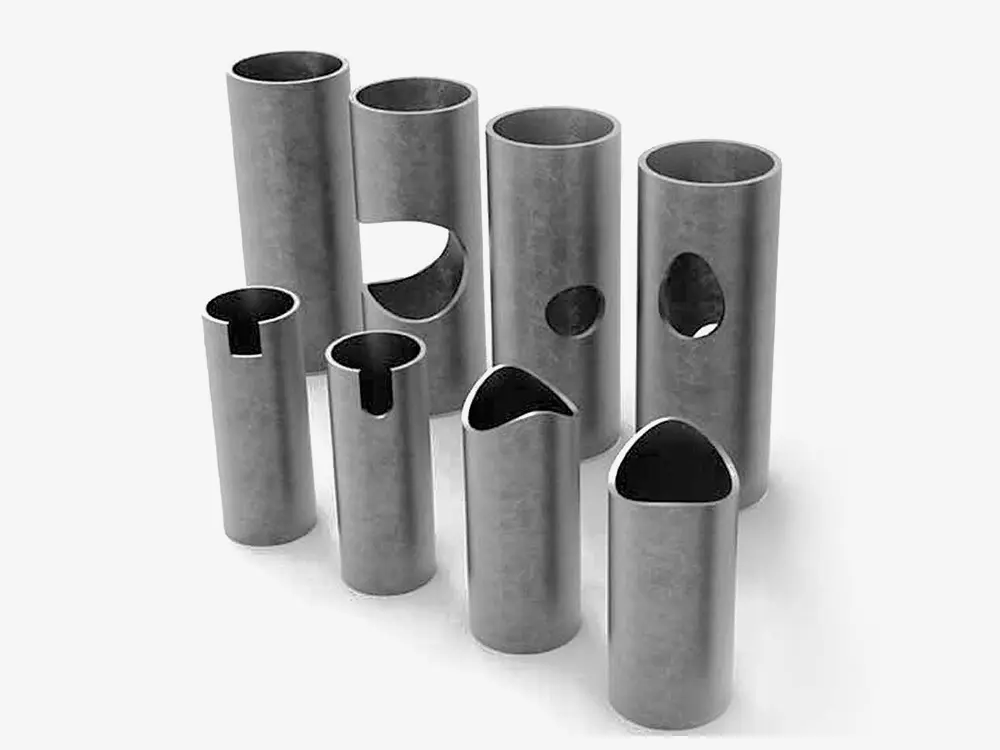
Machine Configuration
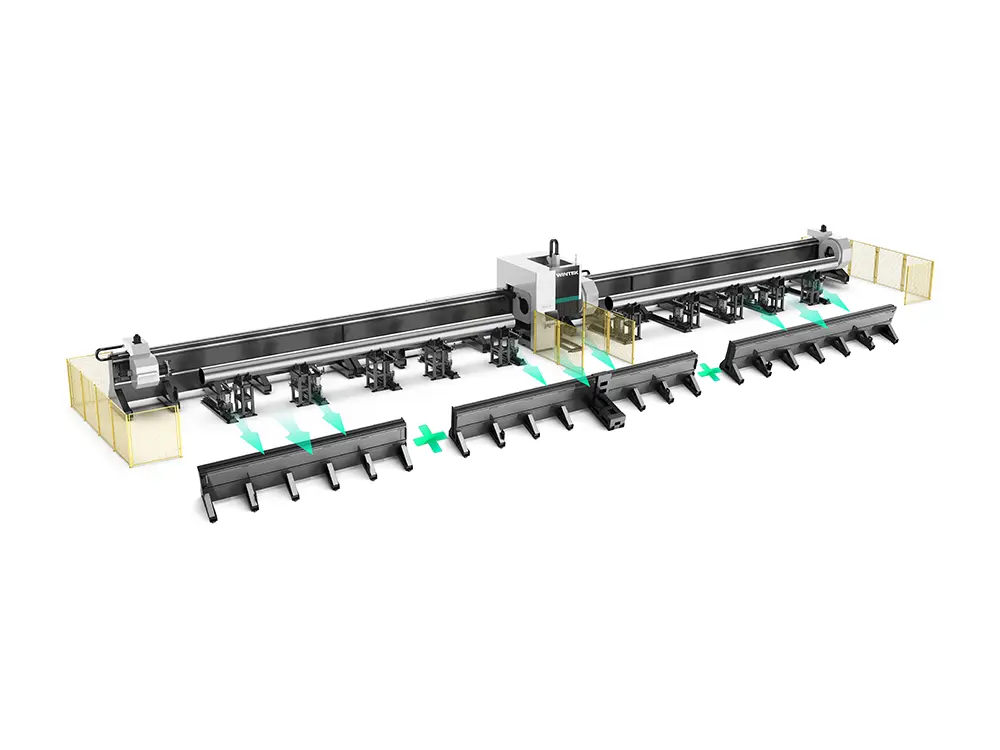
Segmented Side-Mounted Bed Structure
The segmented side-mounted bed features high load-bearing capacity and strong stability, making transportation, loading, and unloading more convenient. With coaxial processing, it ensures high cutting precision and smooth operation.
Full-Length Pipe Processing
Supports 12m full-length pipe loading and cutting, eliminating the need for secondary processing of long pipes, and ensuring high efficiency and increased productivity.
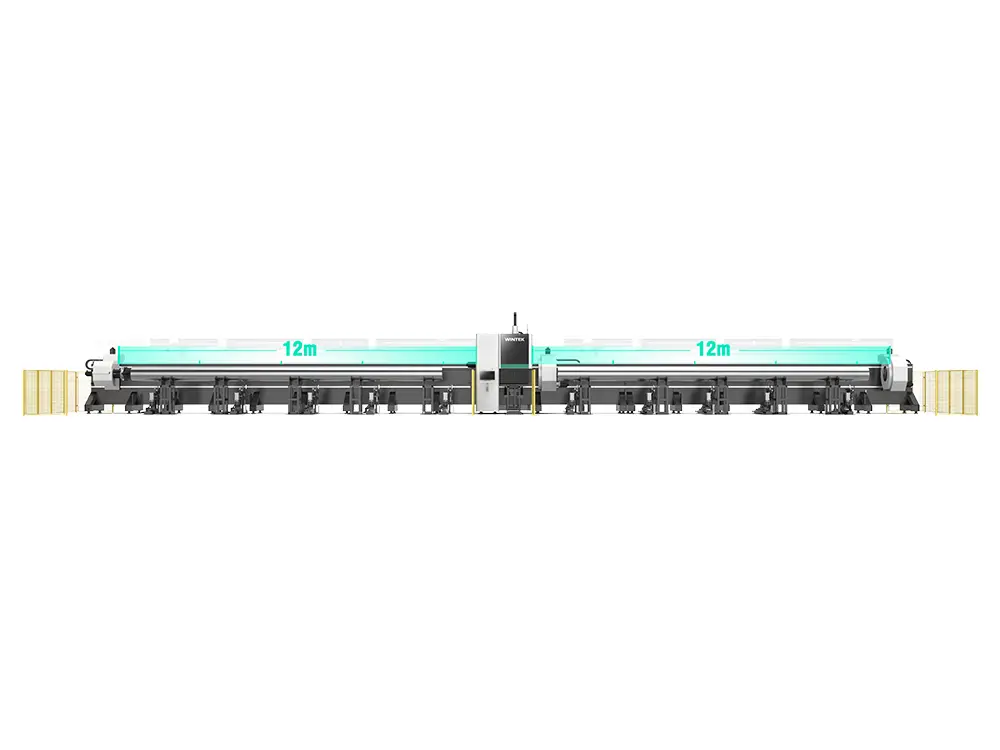
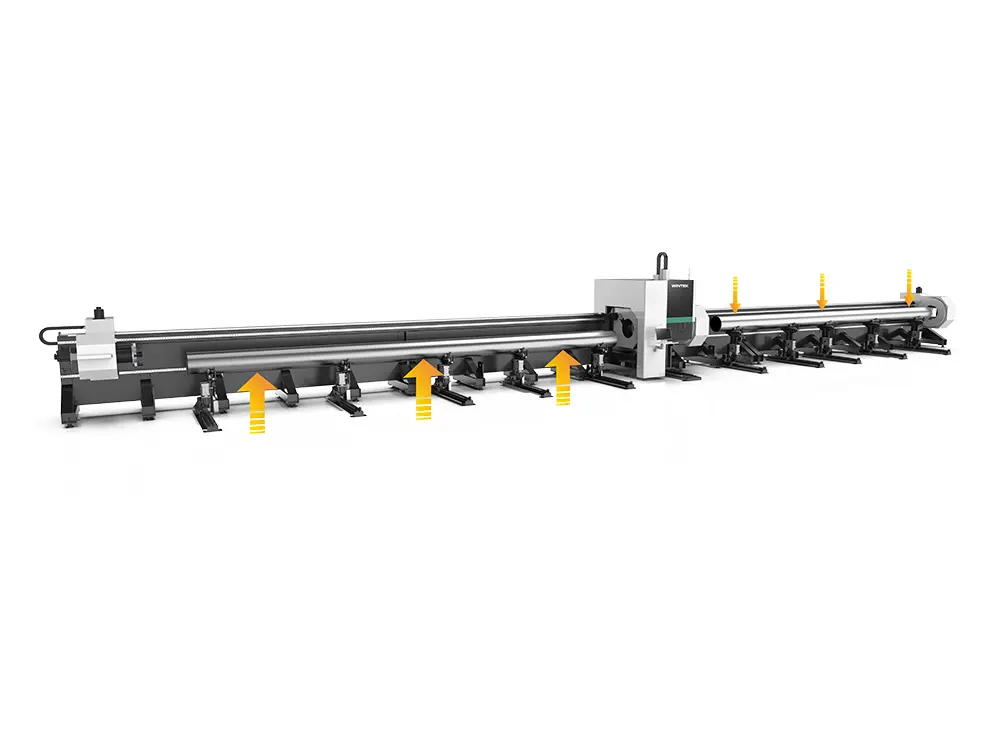
Single-Pipe Loading and Unloading Device
The single-pipe loading and unloading device enables synchronized loading and unloading, ensuring operator safety during the unloading process while significantly enhancing production efficiency.
Multi-Pipe Loading and Unloading Device
An optional multi-pipe loading and unloading unit ensures high efficiency, smooth, and impact-free material handling, supporting multiple pipe and profile types.
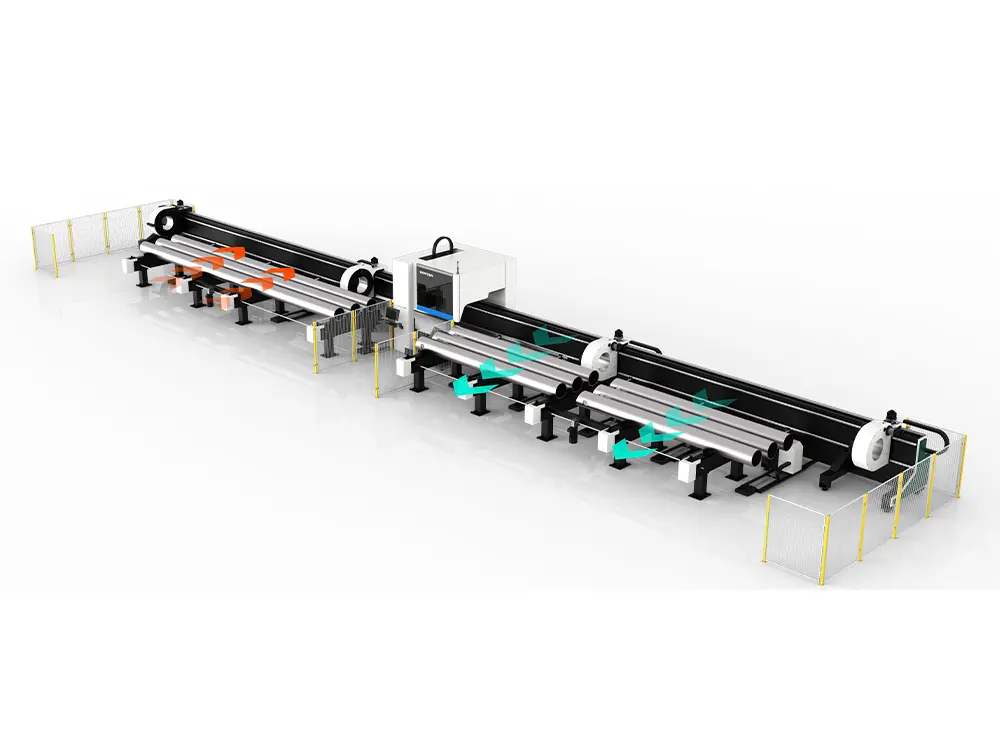
Tube Laser Cutting Machine - Other Core Components
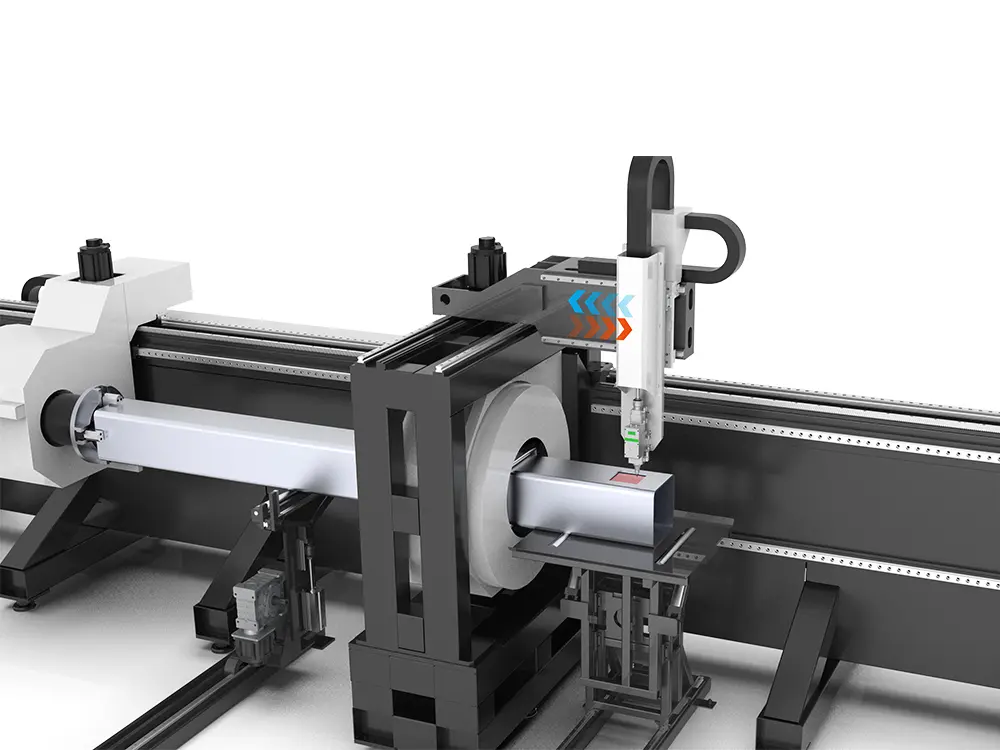
Static Precision High-Speed Cutting
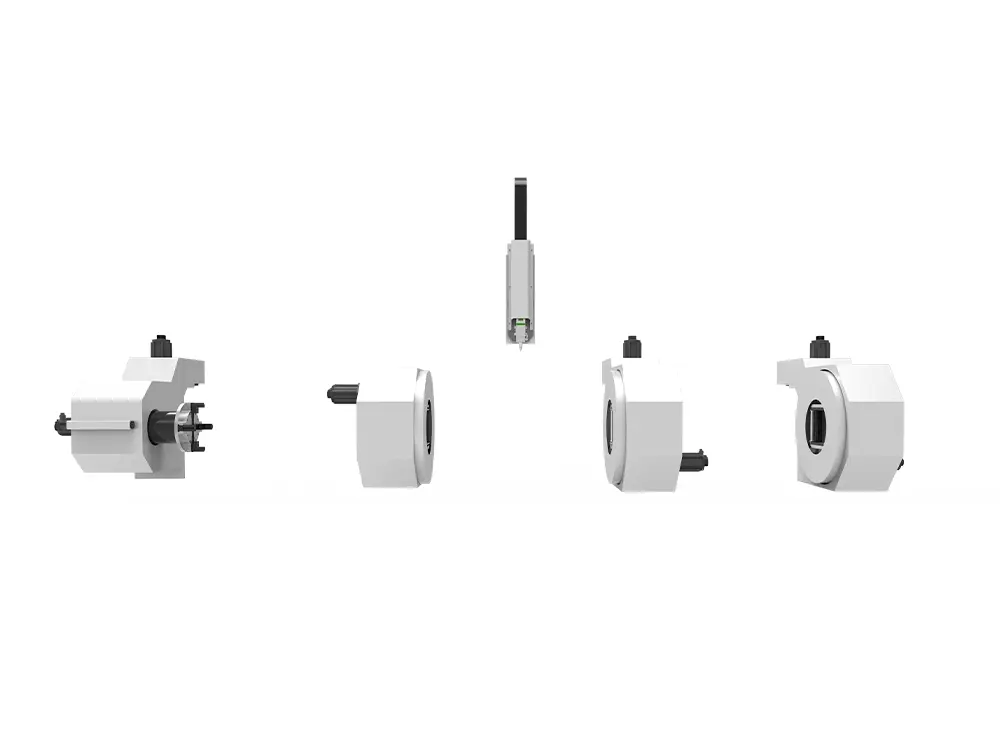
Heavy-Duty Four-Chuck Design
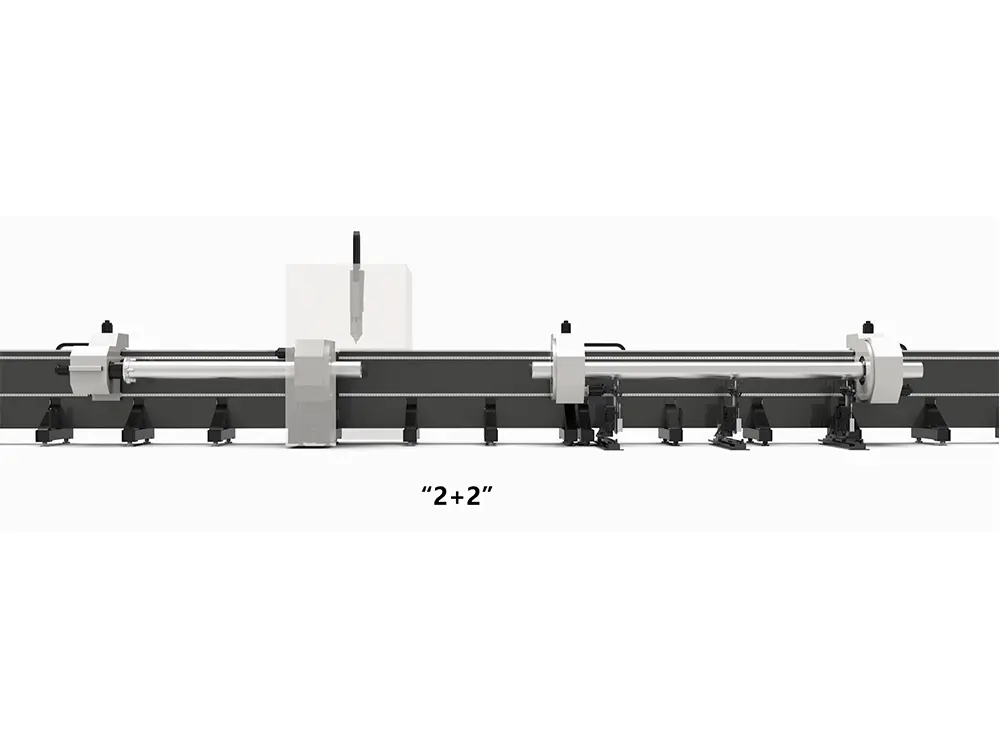
“2+2” Processing Mode
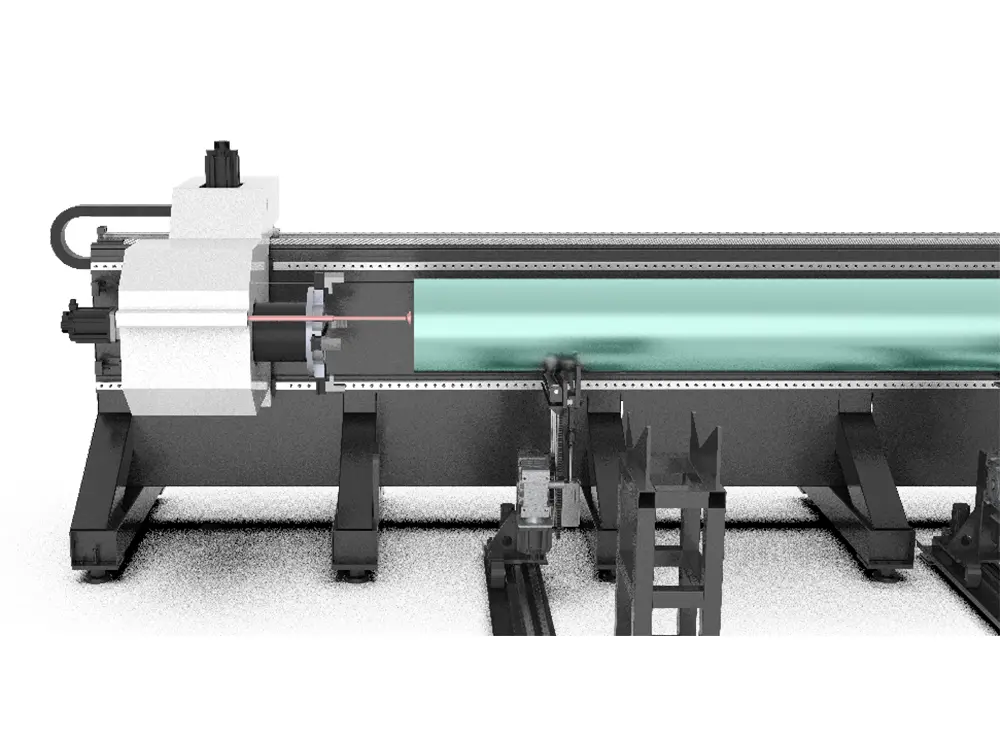
Automatic Pipe End Detection System
Tube Laser Cutter Benefits
1. Enhanced Clamping Stability: The four-chuck structure provides simultaneous clamping at both ends of the pipe, ensuring stable support and improved cutting precision. This minimizes material movement, making it especially suitable for long or irregularly shaped pipes.
2. Reduced Material Waste: Unlike traditional chucks requiring longer pipe tails for clamping, the dual-end clamping of four-chuck machines effectively shortens tail material, increasing material utilization and reducing production costs.
3. Versatility for Various Materials and Shapes: The four-chuck design accommodates round, square, rectangular, and irregularly shaped pipes, supporting a wide range of sizes and materials such as carbon steel, stainless steel, and aluminum, expanding its application scope.
4. Improved Processing Efficiency: With dual chucks operating simultaneously, clamping speed and processing efficiency are significantly enhanced. The efficient rotation and feeding of materials reduce overall production time, making it ideal for mass production.
5. Optimized Cutting Precision: The synchronized clamping function of four chucks minimizes cutting errors caused by material vibration or misalignment, delivering high-precision results that meet stringent production standards.
6. Seamless Automation Integration: The four-chuck design integrates seamlessly with fully automated loading and unloading systems, enabling unmanned operation. Automatic adjustment and clamping functions further reduce manual intervention, boosting production efficiency and equipment utilization.
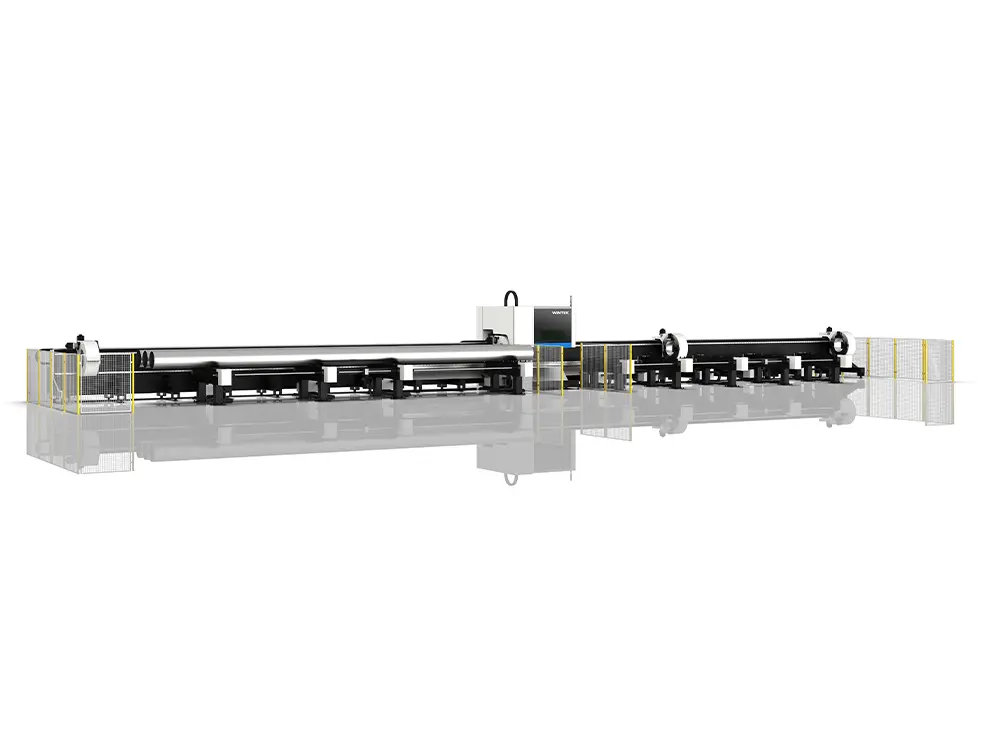
Feel free to contact us now for more details!
Our team is ready to provide you with tailored solutions and support.